Molten Salt Reactors
A Molten Salt Reactor (MSR) is a specialised chemical reactor designed to operate with molten salts as either a solvent, heat transfer medium, or reactant. These systems are typically used for extremely high-temperature processes and offer unique advantages in energy efficiency, heat transfer, and reaction control. With safer, more energy efficient systems with the potential for breakthroughs in areas like materials processing, waste recycling and next-generation power, Molten Salt Reactors are a hot topic.
Molten Salt Reactors use inorganic salts (such as chlorides, fluorides, or nitrates) which are heated until they melt and used as a liquid reaction medium. The molten salts provide a stable and often inert environment, making them suitable for:
- High-temperature organic synthesis
- Inorganic reactions
- Electrochemical processes
- Metal refining
- Catalysis studies
- Materials science and nuclear applications
Molten Salt Reactors are most often a single cell reactor (commonly sized between a few mL and 1 L), however it is possible to work in parallel. Some systems utilise a kind of “twin” vessel, with salt boiled in the first vessel up to 800 °C (temperature required depends upon reactant) until it reaches a molten state, then gaseous vapours travel into this “twin” or receiver vessel where the salts are captured, having gone through a resin column filtration system.
Heating can be external (jacketed) or internal, however the degradation of internal heating apparatus is considerable due to the effects of the salt crystallisation.
This type of reactor is commonly associated with the early Molten Salt Nuclear Reactor – developed in the 1950s and 1960s as part of research at Oak Ridge National Laboratory (ORNL) in the United States.
If you’d like further information, or to discuss how a Molten Salt Reactor would benefit your research, please contact us.
- Operating temperature: typically 200 °C to 1,000 °C
- Materials of construction: often high-nickel alloys (such as Hastelloy), ceramics or quartz to resist the inherent high levels of corrosion.
- Reactor type: batch or flow configurations, usually with heated jackets or immersion heaters.
- Inert atmosphere: often uses nitrogen or argon to prevent oxidation.
- Visual form: batch or flow configurations, usually with heated jackets or immersion heaters
- Pressure rating: this can vary depending upon requirements, commonly designed to 10 barg working pressure however.
- Wide range of manufacturing customisation to suit your chemistry.
UK / Europe / Global Delivery
Developed in collaboration with our clients / Bespoke design service
Committed to developing sustainable & practical improvements for scientists worldwide
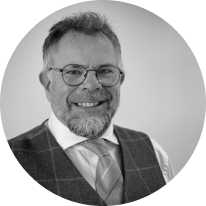
Martyn Fordham, MD